Cargo news
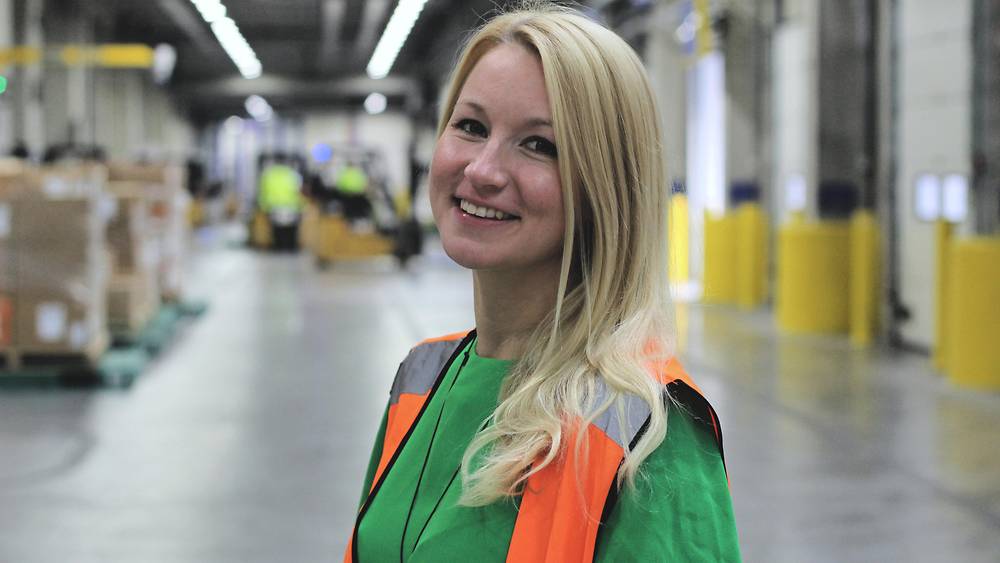
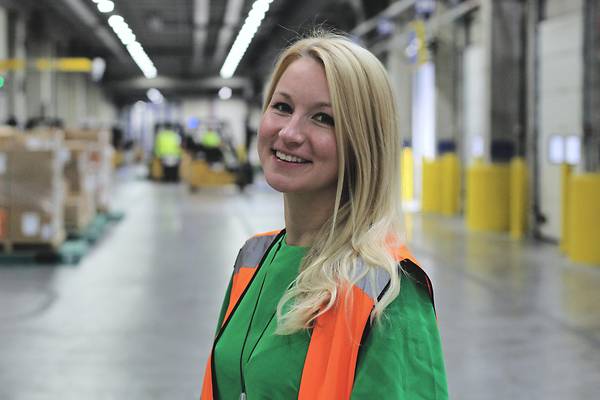
Janike, Network Supervisor: "I enjoy making decisions under pressure and I love the daily speed of operations"
Janike Heimonen is a Network Supervisor working at Finnair Cargo’s state-of-the-art COOL Nordic Cargo Hub. Peter Seenan talked to Janike to understand more about how her work directly impacts the flow of air cargo around the globe each day.
“The best things about my work as a Network Supervisor are the responsibility, working environment and people, and development – by that I mean both personal development and how we improve and develop Finnair Cargo’s operations.
I enjoy making decisions – especially under pressure – and I love the daily speed we have in our operations.
To give you an example, part of the daily life of a Network Supervisor involves making decisions on the go, in other words, deciding what to do when things don’t go exactly to plan. These can be quite major things or smaller deviations.
There are various examples of irregularities which any air cargo carrier can face daily the world over. These might be aircraft changes, delays, weather causing minor disruptions, lots of passenger bags on a flight – we operate belly cargo – or trucks arriving late.
There are also more serious events that impact Finnair operations on a wider level. Extreme weather conditions are a typical example of something that can have a major impact to Finnair traffic.
In all these different situations, we talk, plan and execute with Finnair Cargo Duty Managers here at the COOL terminal. And when there are Finnair Group-wide meetings the Duty Managers represent Finnair Cargo and our customers.
Taking proactive and corrective actions and constantly ensuring a high standard of service is a central part of my work.
Most of the time things go very smoothly, but when there are small deviations – like a shipment that has been marked by a customer with the wrong special handling code – then corrective actions must be taken.
As network supervisors we report on deviations and then make operations and commercial decisions closely with the COOL Control Center, cargo network partners and our sales team. A truck arriving late means that there might have to be re-prioritisation of shipments.
A proactive action could be, for example, what we call a “landside steering” decision, such as checking in shipments the night before so we’re already a step ahead of the next day’s operations.
My daily responsibilities include checking that booked shipments have arrived by the latest acceptance times and monitoring warehouse operational targets to ensure everything is working smoothly, in other words, ensuring that cargo is flown as booked (FAB).
Every day is different – so far during my time here there hasn’t been a single day that was the same as another.
The recent Japan typhoon was impactful and as network supervisors we’re responsible for monitoring and adjusting cargo flow network-wide.
In this situation there were some delays and flight cancellations; the typhoon caused the closure of Osaka airport but in collaboration with our global sales team and revenue yield management (RYM) team we were able to re-route shipments to other airports in Japan so it caused as little disruption as possible to customers.
One aspect of my job that is constant is the fact that we speak every day to our RYM team to discuss cargo capacity and other important day-to-day details.
In this picture I am using one of our tools to plan the flights. Being responsible for flight planning means planning what cargo goes on a ULD (A Unit Load Device is loaded into the cargo hold of a plane and on it will be stacked various shipments). And for example, ensuring high priority shipments go on the same ULD. I work with a colleague who has the job title Workstation planner. That person manages the process of dividing tasks among staff on the terminal floor to ensure these jobs are completed.
On the big screens I can see the progress of the build-up and break down jobs and a live picture from COOL terminal. I’m in the COOL Control Center which is in the same building as the COOL terminal, so if I want to see things with my own eyes I can get up and walk to the terminal floor, which takes a matter of seconds.
We use different digital tools for steering, pre-planning and what we call on-time planning.
For example, SkyChain shows bookings, Cargo Eye enables us to monitor incoming trucks, and a warehouse operations system integrated with SkyChain helps with ULD planning and the task division at workstations.
In our role as Network Supervisors we are also responsible for making development proposals based on the operational and commercial performance.
This is something that is very close to my heart because I love to enhance and make things better and take things to a new higher level. I am fascinated by the complexity of the aviation industry. New proposals come from what we observe during daily operations and we pay close attention to what can be optimised.
Network supervisors work together with the likes of sales and the COOL Control Center, the support team and warehouse operators to improve performance. One example would be how we’ve improved narrow-body operations recently.
It is all about the people.
I am thankful for the great people we have at Finnair Cargo. We have gone through a big transformation at Finnair Cargo changing from the old manual terminal to an automated warehouse and as everyone knows, change is never that straightforward, but the people at Cargo have shown that by supporting one another it is possible."